WMS führt Material- und Informationsflüsse ohne ERP zusammen
Durch eine intralogistische Gesamtlösung von Jungheinrich, deren Kern ein Warehouse-Management-System (WMS) mit Logistik-Interface und Lagernavigation bildet, hat Streng Plastic ihre Prozess- und Arbeitssicherheit und ihre Wirtschaftlichkeit nachhaltig gesteigert. Zu den weiteren Vorteilen zählen eine hohe Bestandstransparenz und eine minimierte Fehlerquote.
Das neue Lager von Streng Plastic beherbergt das 500 bis 700 Artikel umfassende Sortiment. Diplom-Ingenieur Urs Hänseler, stellvertretender Geschäftsführer und Leiter Technik der Streng Plastic AG, Niederhasli, breitet Fotos auf dem Besprechungstisch aus. «Wie die Bilder zeigen, lag unser Material früher teilweise im Freien. Ausserdem haben wir es in Paletten- und Kragarmregalen sowie auf dem Boden in Gitterboxen gelagert und daraus in Plastiksäcke kommissioniert. Die Nachteile haben in unübersichtlichen Beständen, einem beträchtlichen Personal- und Suchaufwand sowie im Platzmangel gelegen.» Schliesslich gewährt Hänseler einen Blick in das Pflichtenheft. «Wir haben mehr Wirtschaftlichkeit, Prozess- und Arbeitssicherheit, Transparenz und Zuverlässigkeit angestrebt. Erreichen wollten wir diese Ziele in erster Linie durch ein WMS. Die Software sollte ein reibungsloses Zusammenspiel unserer intralogistischen Abläufe garantieren, Bestands- und Kostensenkungen sowie kürzere Durchlaufzeiten ermöglichen und somit unsere Effizienz erhöhen.»
Zukunftsweisende Lösung
Da der Betreiber noch ein älteres ERP-System einsetzt, hat er seine intralogistischen Prozesse via WMS und von dort über eine definierte Schnittstelle an sein Host-System anbinden lassen. Eine zukunftsweisende Lösung, die den Austausch von Artikelstammdaten, Warenein- und -ausgangsavis, Bestandsabgleichen oder Kommissionierstatus erlaubt. Basierend darauf kann Streng Plastic autark mit dem WMS arbeiten, ohne das ERP-System in die operativen Abläufe einbeziehen zu müssen und – strategisch bedeutsam: Streng kann beim ERP neue Releases oder gar ein komplett neues ERP-System mit überschaubarem Aufwand und sehr geringen Risiken einführen.
Das Jungheinrich WMS führt die Material- und Informationsflüsse zusammen und optimiert sie. Beispielsweise deckt es ungenutzte Potenziale in der Verwaltung und Steuerung des Lagers auf. Und ein umfassendes Berichtswesen mit individuellen Auswertemöglichkeiten bildet die Grundlage für eine durchgängige Transparenz.
Auf die Anwendung massgeschneidert
Für den Einsatz bei Streng Plastic hat Jungheinrich sein modulares WMS massgeschneidert konfiguriert. So hat das Unternehmen die Standardausstattung ergänzt, zu der umfangreiche Funktionen der Lagermodellierung, eine zentrale Stammdatenverwaltung und verschiedene Inventurvarianten zählen. Ein weiteres Beispiel ist die Steuerung der Materialflüsse, etwa im Warenein- und -ausgang, im Lager sowie in den Reserve- und Kommissionierbereichen. Hinzugekommen sind die Module Staplerleitsystem, Lagervisualisierung, Logistik-Interface und Hostschnittstelle. Zudem ist das WMS projektspezifisch parametriert worden.
Logistik-Interface «übersetzt» Fahraufträge
Urs Hänseler entfaltet eine Zeichnung der Lagerbereiche, die ausnahmslos in das WMS integriert sind. «Wir arbeiten im Wesentlichen mit einem Schmalganglager, das über 4100 Palettenplätze verfügt und einen hohen Raumnutzungsgrad bietet. Eingelagert wird gemäss ABC-Kriterien und dabei nach Prioritätssteuerungen, die im WMS hinterlegt sind. In der Kommissioniergasse liegen Komponenten, die zusammengehören, nebeneinander.» Von den 6 etwa 20 bis 50 Meter langen Schmalgängen ist einer als Kommissioniergang ausgelegt. In einem Teil der Halle dient ein Kragarmregal zur Lagerung von Kunststoffplatten und anderen sperrigen Materialien.
Bei den im Schmalganglager eingesetzten Flurförderzeugen handelt es sich um einen induktiv geführten Elektro-Kommissionier-Dreiseitenstapler EKX 515, der täglich rund 100 Ganzpaletten bewegt, und um einen Vertikalkommissionierer EKS 210, für den am Tag etwa 150 Einzelentnahmen im Rahmen von 10 bis 20 Kommissionieraufträgen anfallen.
Fahr- und Kommissionieraufträge halbautomatisch abfahren
Da Jungheinrich die Flurförderzeuge mit RFID-Lagernavigation versehen hat und sie mit dem WMS kommunizieren lässt, werden ihre Fahr- und Kommissionieraufträge halb automatisch abgearbeitet. Eine wichtige Rolle spielt hierbei das Logistik-Interface, das die Systemfahrzeuge mit dem WMS verbindet. Diese speziell entwickelte Middleware «übersetzt» die Fahraufträge, die der WMS-Client auf dem Fahrzeugterminal empfängt, und sendet sie direkt an die Staplersteuerung. Daher «kennt» das Gerät, das aufgrund der im Boden integrierten Transponder «weiss», wo es ist, auch den nächsten anzufahrenden Lagerplatz. Der Bediener, dem die Software auf seinem Display die Fahrt- und Hubrichtung visualisiert, muss bloss noch den Fahrimpuls geben. Das Flurförderzeug fährt sein Ziel daraufhin diagonal auf dem schnellsten Weg punktgenau an. Erledigte Arbeitsschritte bestätigt das Logistik-Interface automatisch an das WMS. Die Vorteile liegen in einer deutlich gesteigerten Effizienz, die sich in bis zu 25 Prozent mehr Leistung beim Ein- und Auslagern und in einer hohen Pickqualität zeigt. Hinzu kommen ein spürbar geringerer Energieverbrauch, eine ergonomische Entlastung des Bedieners und eine Zeitersparnis, weil Such- und Korrekturfahrten sowie manuelle Kontrollen durch Scannen entfallen.
An beliebige Lagerverwaltungssysteme anbindbar
Über das Logistik-Interface können Jungheinrich-Flurförderzeuge an beliebige Lagerverwaltungssysteme angebunden werden. Um über diese standardisierte Schnittstelle mit den Fahrzeugen zu kommunizieren, muss das System nicht oder nur sehr leicht angepasst werden. Zudem lässt sich das Logistik-Interface neben Standardanwendungen, wie der RFID-Lagernavigation, zum Beispiel für Ortungen und in Kombination mit Automatikscannern nutzen.
Eine Voraussetzung für den Einsatz eines WMS zum Steuern von Flurförderzeugen ist Datenfunk. Urs Hänseler präsentiert die Zeichnung einer WLAN-Simulation des Lagers. «Hier wird ersichtbar, dass acht Access Points zu installieren waren, um das Lager komplett mit Funk ausleuchten und unsere drei Fahrzeuge, vier Handterminals und den Funkscanner überall anbinden zu können.» Die daraus resultierende Prozesssicherheit und Verfügbarkeit der Lagernavigation ist laut einer Funkmessung und Performance-Analyse gewährleistet.
Hänseler blättert in einer Statistik. «Die Fehlerquote hat, bezogen auf alle Aufgaben, stark abgenommen, weil das WMS die Mitarbeiter entsprechend entlastet. Davon profitieren wir hauptsächlich dann, wenn nach mehreren Stunden die Konzentration nachlässt. Insofern kommen wir heute, trotz grösserem Auftragsvolumen, mit gut zwei Dritteln der früher benötigten Personalstärke aus.»
Strukturiert projektiert
Die Herausforderungen haben für Jungheinrich in einem komplexen Gesamtprojekt mit vielen Gewerken gelegen, bei dessen Planung ein beschränktes Raumangebot zu berücksichtigen war. Hänseler begleitet eine Palette, die ein Elektro-Dreiradstapler EFG 213, der mit einem Fahrzeugterminal und Scanner ausgestattet ist, vom Wareneingang zum Schmalganglager fährt. Dort lagert sie der Kombistapler EKX 515, geführt durch die Lagernavigation, bis auf eine Höhe von maximal 9 Meter ein. Die zwei Transportstufen für die Einlagerungen berechnet das Staplerleitsystem jeweils vorab.
Nach diesem Lagerspiel stapelt der EKX 515 eine andere Palette in die Kommissioniergasse um, wo ein Mitarbeiter Aufträge mithilfe des Vertikalkommissionierers EKS 210 zusammenstellt. «Anhand unseres Datenflusses und des daraus resultierenden Materialflusses kann man sich denken, was wir unter Prozesssicherheit verstehen.»
Als Generalunternehmer alles aus einer Hand
Jungheinrich hat die intralogistischen Prozesse analysiert, Ablaufstrukturen aufgebaut und als Generalunternehmer alles aus einer Hand geliefert. Hänseler hebt die schnelle, zuverlässige Realisierung des Projekts ohne Schnittstellenprobleme hervor. Er habe kompetente, verlässliche Ansprechpartner gehabt. Ferner habe Jungheinrich Streng Plastic weit über die eigenen Produkte und das Abnahmedatum hinaus unterstützt. Das gelte auch im Hinblick auf den Hallenboden, der beim Einsatz von Schmalgangstaplern sehr eben sein muss.
Nach einer Projektdauer von nur 22 Wochen hat die Intralogistiklösung ihren Betrieb im Mai 2012 aufgenommen. Hänseler streicht die Zeichnung des Lagers glatt. «Wir haben das Projekt in partnerschaftlicher Zusammenarbeit und unseren Anforderungen entsprechend termingerecht und erfolgreich umgesetzt. Das Konzept für das Warehouse-Management-System hat im Wesentlichen binnen zwei Tagen gestanden. Uns hat die gelungene Kombination der Teilgewerke überzeugt und dass Jungheinrich für alle Gewerke den durchgängigen Sicherheitsnachweis erbringen konnte.» Ausserdem habe sich Jungheinrich auf die gewünschte Lackierung der Regale in Weiss und der drei Flurförderzeuge in Purpurrot eingelassen. Und als die für den Brandschutz zuständige Behörde nachträglich verlangt hat, eine separate Halle für die Batterieladestation zu errichten, habe Jungheinrich eine unkritische Konzentration an Schwefelwasserstoff nachgewiesen.
Urs Hänseler lehnt sich zufrieden in seinem Stuhl zurück. «Am Anfang haben wir mit dem Lager Neuland betreten, dann folgte eine steile Lernkurve. Jetzt, nach eineinviertel Jahren Betrieb, sind wir sogar leistungsfähiger als geplant.»
Streng Plastic: Spezialist für Kunststoffrohrleitungssysteme
Die 1954 gegründete Streng Plastic AG mit Hauptsitz in Niederhasli, führt ein breites Sortiment an Kunststoffrohrleitungssystemen. Das Unternehmen, das alle Produkte an den Standorten Niederhasli und Dielsdorf selbst herstellt und über einen eigenen Handel verkauft, beliefert Kunden aus den Bereichen Abwassertechnik, Wasser- und Gasversorgung und Kabelschutz. Bei den Abnehmern handelt es sich vornehmlich um Schweizer Unternehmen, aber auch um Kunden aus anderen europäischen Ländern. Streng Plastic erwirtschaftet mit 120 Mitarbeitern einen Jahresumsatz von gut 50 Millionen Schweizer Franken.
Jungheinrich AG Schweiz
Führend in Europa im Bereich Lagertechnik, gehört Jungheinrich weltweit zu den drei grössten Anbietern von Flurförderzeugen, Lager- und Materialflusstechnik. Mit Konzernsitz in Hamburg erfolgt der Direktvertrieb für die Schweiz aus Hirschthal im Aargau. Jungheinrich ist mit den vier Geschäftsfeldern Flurförderzeuge, Logistiksysteme, Miet-/Occasionsstapler sowie Kundendienst ein kompetenter Partner und Gesamtanbieter rund um die Intralogistik.
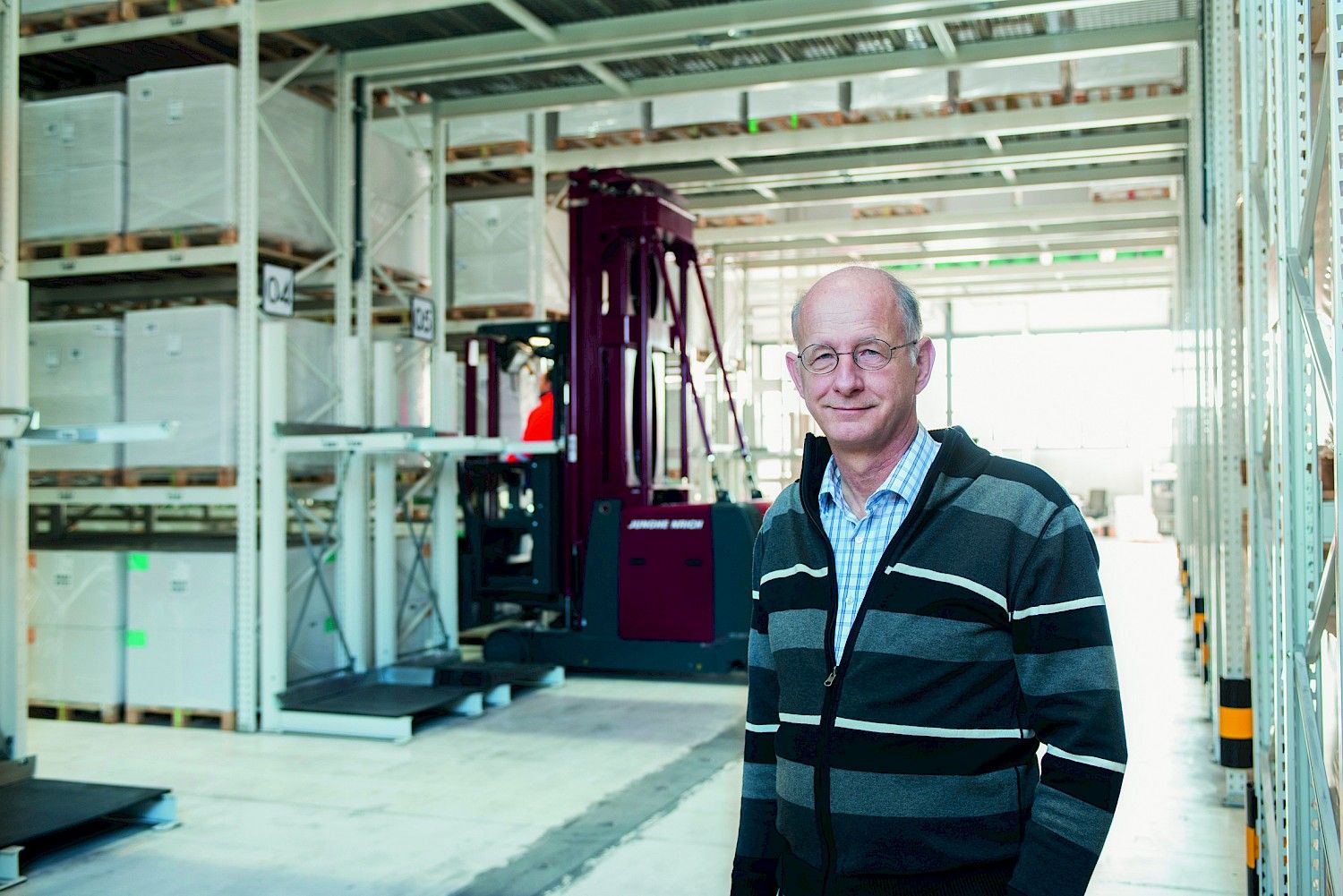
Urs Hänseler, stellvertretender Geschäftsführer und Leiter Technik der Streng Plastic AG, Niederhasli.
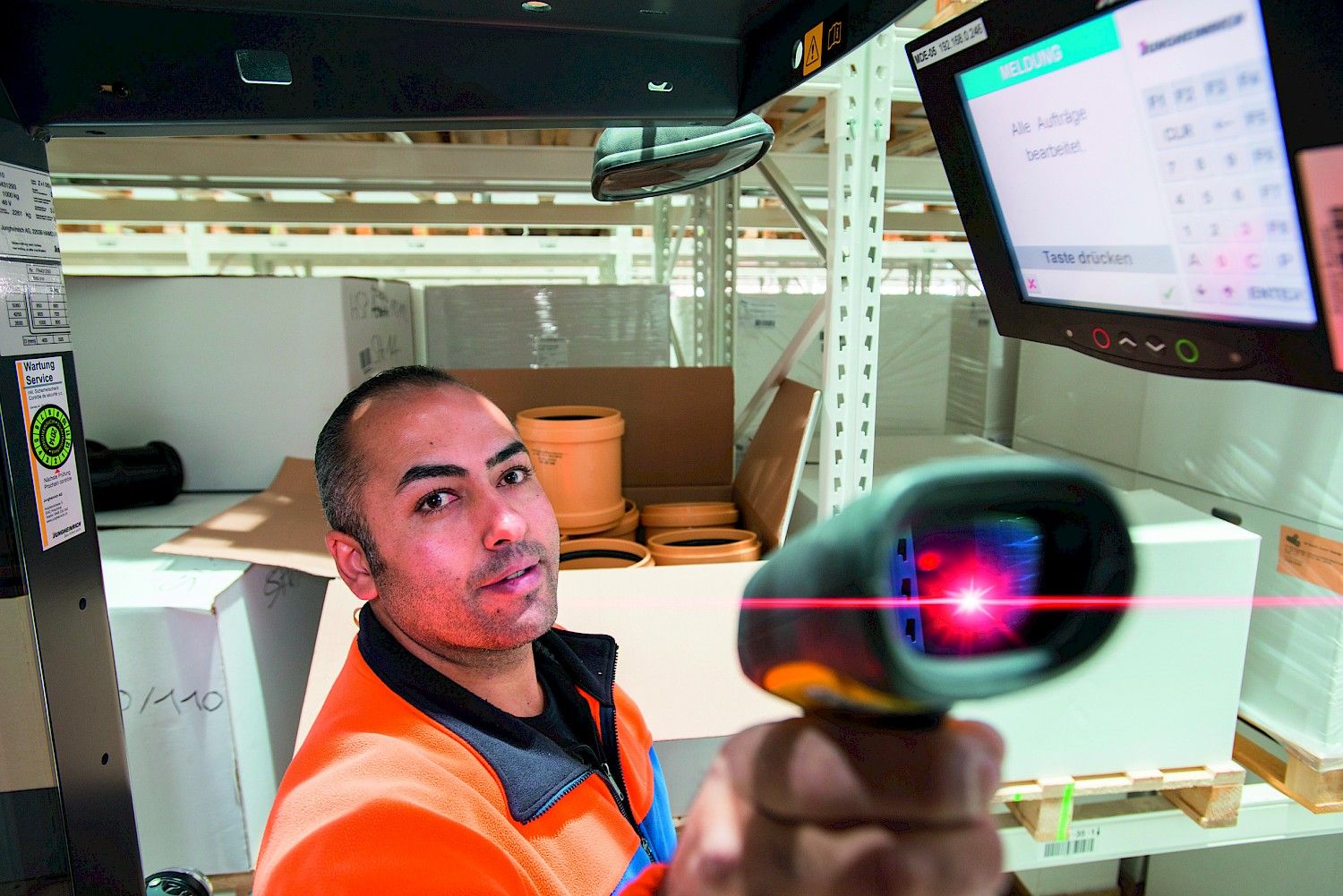
Ein- und Auslagerung im Lager mit Hand- oder Automatikscannern.
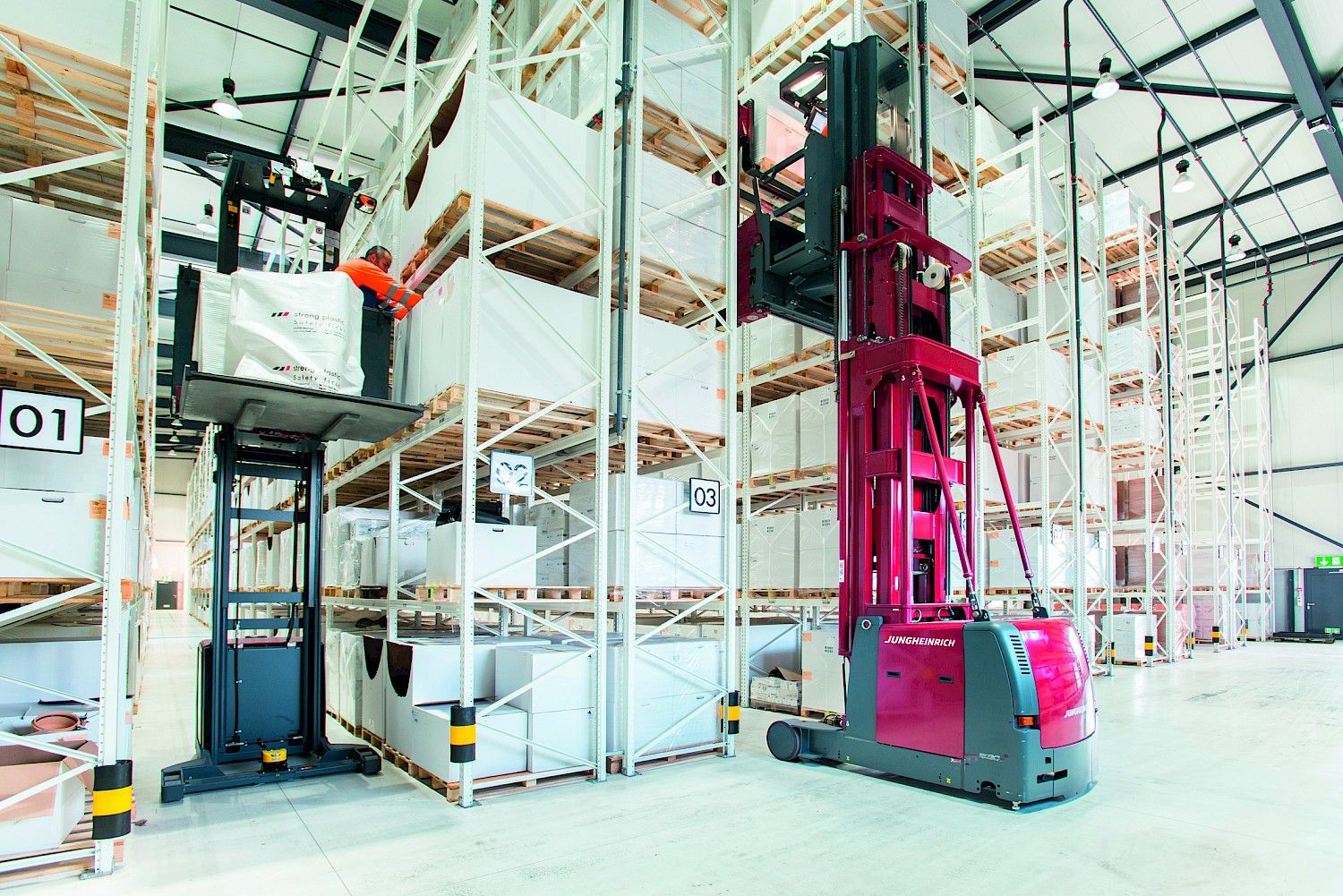
Das Schmalganglager verfügt über 4100 Palettenplätze und bietet einen hohen Raumnutzungsgrad.
Kontakt
Jungheinrich AG
Holzikerstrasse 5
5042
Hirschthal
Schweiz
(CH)
Tel: 062 739 31 00
Fax: 062 739 32 99
info@jungheinrich.ch
http://www.jungheinrich.ch